Blood bags are lifesaving critical medical devices. In this blog, we have detailed the process of manufacturing blood bags. We have also provided an overview of the Indian blood bag market. This will help you determine whether you should start a blood bag business in India.
What is a blood bag?
Blood bags are used for collection, storage, and infusion of blood. These medical devices are specially designed to be contamination and coagulation free and leak proof. The main component of this medical container is a deformable hermetically sealed bag to collect the blood. Additionally, it has a diaphragm sealed delivery tube and a collecting line made of flexible tubing. Needle, needle cover, and clamps are also a part of this critical medical device. These apparatuses are specially designed to be flexible enough for filling of blood, transfer of components, and complete emptying without venting.
The bag and its parts are manufactured using bio-compatible materials. Anticoagulants and other additives are used while constructing these bags. Furthermore, these bags should be able to withstand low temperatures. Additionally, the bag should not contain or release any toxic substances into the collected blood that may harm the recipient. Also, these bags are designed to pose no contamination or air embolism risk, which is essential for safe blood transfusion. Thus, blood bags are used for safe collection, storage, and administration of whole blood and its components.
Types of blood bags:
- Single Blood Bag
- Double Blood Bag
- Transfer Bag
- Platelet Storage Bag
- Top and Bottom Triple Blood Bag
- Top and Bottom Quadruple Blood Bag
The above list presents some of the commonly used blood bags. Single blood bags are an easy-to-use medical device for safely collecting, storing, and transferring blood samples. Whereas, double blood bags are used for collection and separation of whole blood into two blood components: plasma and red blood cells. Triple blood bags have a further added feature. They are used to separate whole blood into three components, red blood cells, platelets, and plasma, by centrifugation and extraction. Triple top and bottom blood bags are also used to collect and separate three blood components. These bags are used to separate plasma, red blood cells, and buffy coat.
These specialized medical containers have a vital role in medical emergencies. They are the back bone of blood transfusion in critical conditions. Blood bags facilitate a secure and effective blood supply for diverse medical procedures These durable containers are used by healthcare providers to collect donated blood and process it into components. Then, they are stored and transported to patients in need.
Manufacturing blood bags
Machinery and equipment required
Some basic equipment required for manufacturing blood bags:
- Extruder
- Film Blowing Machine
- Cutting Machine
- PVC Welding Machine
- Steam Sterilizer
- Profile Extrusion Dies
- Pumps
Raw materials
Basic raw materials required for manufacturing blood bags:
- PVC pellets
- PVC tubing
Manpower required for operating the blood bag manufacturing facility
- Skilled technicians to operate the machinery
- Supervisors
- Experienced quality control personnels
- Plant operators
- Helpers and assistance
- Security personnels
- Sales person
- Accountant
- Manager
An industrial area will be required for setting up the blood bag manufacturing facility. Dedicated medical device assembly, sterilization, and storage units will be required. Adequate power and water supply along with proper waste disposal units will be required.
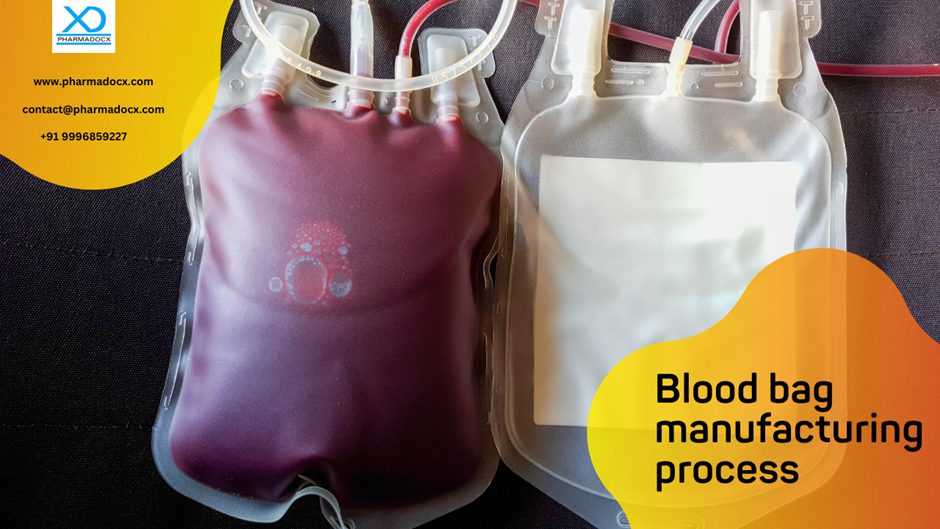
Blood bag manufacturing process
We have already listed the requirements for manufacturing blood bags. Now, we will present in details how to manufacture blood bags. The blood bag manufacturing process is carried out in a clean environment, as contamination should be avoided while manufacturing them.
- First, the PVC pellets are poured into the extruder hopper. The profile dies of circular shape is mounted at the end of extruder. Then, the barrel heaters are switched on and the temperature is increased till the PVC melting temperature is attained. The PVC pellets in the hopper move into the barrel. The screw in the barrel of the extruder rotates very closely with the stationary barrel. The generated force exerted on the material pushes it forward in the barrel. The heat generated by heating elements and friction heat up the material as it moves through the barrel.
- As a result, the PVC pellets melt. The pressure and temperature at the extruder exit are preset. Once the desired glass transition temperature is attained, the melted material is forced through a die by the extruder into the film blowing machine.
- Air pressure is used to expand the film. After the film expands to the desired dimensions, it is cooled to generate solidified polymers. The cooled PVC polymer films are rolled using rollers. Thus, PVC blown films are manufactured, which is the first step in manufacturing blood bags.
- Then, the film is fed into the cutting machine. The cutting machine cuts the PVC blown films as per required dimensions. Then, these cut films are inserted into the PVC welding machine. The profile dies as per the required blood bag dimension is mounted onto the welding machine.
- Then, the PVC blown films get welded as per the preset shape of the profile die. The excess linings are trimmed and separated.
- Blood bags have to be sterilized to eliminate contaminating microorganisms. Radiation or gas sterilization cannot be used, as anticoagulant and preservative solutions added to blood bags are degraded by radiation/gas. Thus, high-pressure steam sterilization technique is used.
- Finally, the manufactured blood bags have to be tested for safety, quality, and efficacy. Quality control is a vital step in any medical device manufacturing process. Additionally, the ability of blood bags to withstand low temperatures has to be evaluated. This is because blood bags are exposed to temperatures as low as – 70 °C while preparing fresh frozen plasma.
- The last step is to package and label the blood bags properly prior to shipping them for distribution and sale.
Demand for blood bags in India
Will starting a blood bag manufacturing business in India be profitable and beneficial? Let us understand the demand for blood bags in India. We have provided an overview of the Indian blood bag market.
The Indian blood bag market
In the year 2022, the Indian blood bag market was pegged at USD 46.99 million. It is expected to attain a value of USD 66.51 million by 2028. This high demand for blood bags in India can be attributed to the increasing number of invasive surgeries being performed in India.
Market trends:
- Increase in demand for disposable blood bags to avoid the risk of cross contamination and infections
- Rise in number of surgical procedures, trauma cases, and chronic diseases, which require blood transfusions.
- Utilization of blood components has fuelled the demand for double and triple blood bags, which can separate the blood components.
Market drivers:
- A significant rise in number of road accidents that cause severe blood loss requiring immediate blood transfusion.
- Increase in the number of blood transfusion requiring chronic diseases, such as anemia, sickle-cell anemia, hemophilia, lymphoma, leukemia, etc.
- Increase in healthcare spending and advancements in healthcare infrastructure
- Government initiatives, such as the National Blood Transfusion Council and ‘eBloodServices’, promoting awareness about blood donation is also driving the demand.
Thus, a blood bag manufacturing business in India has immense potential.
CDSCO regulations for blood bags
Blood bags are lifesaving medical devices for emergency cases and chronic diseases. The safety of the patient will depend on the safety and efficacy of the blood bag. Thus, the process of manufacturing blood bags in India is strictly regulated by CDSCO. CDSCO is the apex medical device regulatory body. As per the CDSCO medical device classification system, blood bags belong to CDSCO Class C. Hence, the CDSCO medical device license application process for blood bags will be per CDSCO class C guidelines. For guidance on CDSCO manufacturing license application process, simply call/Whatsapp on 9996859227 or email at [email protected].