Regulatory bodies require medical device manufacturers to confirm whether the finished product meets the set regulatory benchmark. Manufacturers need to have strict quality control systems to ensure the devices being manufactured comply with safety and quality requirements. To ensure this, manufacturers need to test the medical device being manufactured. However, testing every single device being manufactured is not possible. Also, in some cases testing the medical device will destroy it or the device cannot be reused. This is where medical device process validation comes into picture. In this case, the focus is the medical device manufacturing process and not the product.
What is medical device process validation?
Medical device process validation is an important aspect of quality assurance. It is the process of establishing sufficient evidence confirming that the medical device manufacturing process maintains the required level of compliance at all stages. The scientific evidence proving the manufacturing process is capable of consistently manufacturing high-quality products has to be documented appropriately. The validation process involves collecting data from the manufacturing process design stage till the production stage. The data collected is thoroughly evaluated. The focus of medical device process validation is the manufacturing process and not the manufactured medical device. The validation has to be designed in a stringent manner to ensure the finished product is likely to consistently meet the required quality specifications.
When do you need to perform medical device process validation?
Validation should be performed on:
- Existing processes that have been altered
- Any new process that is being implemented
- Existing processes that need to be checked on a regular basis
- Existing process showing a downward performance trend or has led to an increase in negative customer feedback
- Existing process that has been expanded either in volume or scope
Additionally, validation should be performed when:
- Analysis of the end-product do not reveal all variations in safety and efficacy that may occur in the finished devices
- It is suspected that the process is barely being able to meet the designated specifications for the device
- Clinical tests would be required to demonstrate the process has generated the desired result or product
These are some examples of when process validation should be carried out.
Which components of the medical device production process require validation?
Common examples of medical device production components that usually need validation:
- Additive manufacturing
- Sterilization and packaging sealing
- Plastic injection moulding
- Clean room ambient conditions
- Heat treating, welding, soldering, painting, etc.
Basic principles of medical device process validation
To ensure that the medical device manufacturing process consistently meets the required benchmark, a robust medical device process validation should be in place. These are some of the basic principles your medical device process validation should be based on:
- Confirm that equipment and instruments are capable of operating within the stipulated parameters
- Perform replicate cycles validating the required operational range of the equipment
- Monitor and regulate the process during routine operation
- Verify the capability of the equipment to operate within parameters
- Revalidate the equipment being used as needed
The medical device manufacturing process validation plan should include: approach to be taken for validating each element, identification of elements to be validated, documentation to be prepared, and responsibilities of the organisation. These are some of the points to consider while developing a process validation plan. Pharmadocx Consultants will help you implement an effective validation plan.
Process validation types
Depending on the production stage, there are multiple types of process validation.
- Concurrent validation: The first three batches of medical devices produced at mass production scale are validated.
- Prospective validation: Validation is performed during development of medical devices prior to production.
- Retrospective validation: In this case, validation is performed retrospectively by collecting data. The data is used to confirm whether the manufactured medical devices comply with the regulatory requirements.
- Revalidation: It is the process of repeating the original validation procedure to check whether the validation status is consistent.
What is the process validation protocol?
Some of the key components to include in the medical device manufacturing process validation protocol:
- Objectives of the validation protocol
- The medical device being manufactured using the particular manufacturing process
- Determine the medical device manufacturing process to be validated
- Quantifiable criteria for validating the process
- Equipment and instrument to be used for the validation process
- Duration of the validation process
Please feel free to contact us for a detailed checklist of components to include in the validation protocol.
The need for medical device process validation
Process validation plays a pivotal role in quality assurance and is a mandatory requirement of many regulatory bodies. The regulatory bodies have even set standards for the validation process. This validation ensures the medical devices which are being manufactured will perform safely and effectively.
- Manufacturers need to have a thorough validation process that can assure the manufacturing process will consistently deliver safe devices. The devices should be able to impart medical benefits and meet user needs.
- Validation ensures the medical devices will effectively perform as intended.
- Validation of the manufacturing process is a mandatory requirement for certain regulatory bodies. This also demonstrates the manufacturer’s commitment to deliver high quality devices.
- Process validation is documented evidence that appropriate quality assurance tests have been performed to assess the manufacturing process.
Hence, validation is a critical part of quality management in the medical device industry. The medical device industry is highly regulated. Thus, ensuring product quality and patient safety is of utmost importance.
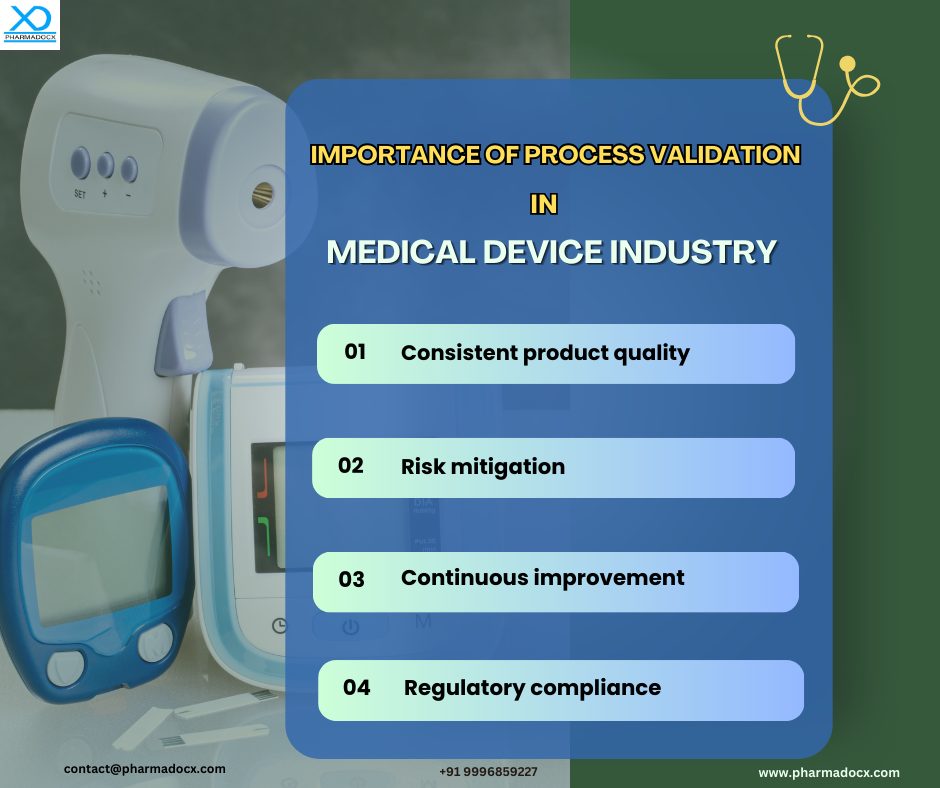
The IQ, OQ, DQ, and PQ in medical device manufacturing
Validation is aimed at ensuring the medical device manufacturing process is stable and performs consistently. The goal is to check that the variation in the manufacturing process is minimal and predictable.
- Installation qualification (IQ) is the process of verifying whether everything is installed correctly.
- Operational qualification (OQ) is the process of verifying whether everything is operating correctly and meeting the predetermined requirements.
- Design quantification (DQ) is the proof of suitability of the design of medical device for the intended purpose.
- Performance qualification (PQ) verifies whether the manufacturing process is stable and the intended results are being produced.
Pharmadocx Consultants: Your process validation guide and support
As a medical device process validation consultant, we provide support and guidance to create validations reports as per regulatory requirements. Our team of experts understands the technical functionality of the manufacturing process. Hence, we are better placed to provide this consultation service. We will ensure your medical device manufacturing process validation is seamless.
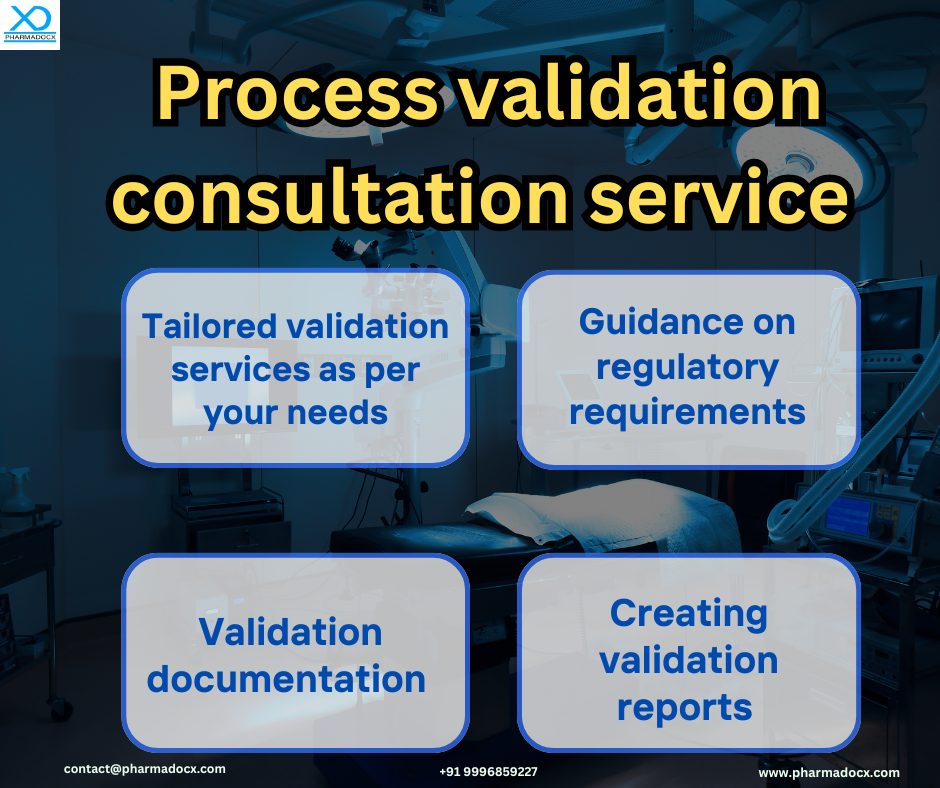
The validation process involves collating information from the design stage till the end of production. The information is evaluated and documented to provide a scientific proof that high-quality and safe products are being consistently manufactured. Medical device process validation has benefits for the manufacturers as well. It assures them that the equipment is functioning properly and they will be able to deliver devices meeting requirement specifications.
Pharmadocx Consultants validation experts will guide you through the process. We will prepare the process validation report in the correct format, as per regulatory requirements, within the stipulated deadline. For more details on our validation consultation services, please contact us. Email us at [email protected] or call/Whatsapp on 9996859227 to get started on medical device process validation.