Clean rooms have a vital role in the medical device manufacturing industry. In the medical device industry, product quality is easily affected by factors, such as airborne particles. Hence, clean rooms are required to maintain a sterile and clean environment. Moreover, the rooms have to abide by strict regulations, such as ISO 14644 guidelines. These guidelines mention the amount of particulate matter permissible in this controlled environment. They also outline the tests that have to be carried out to validate the effectiveness of clean rooms. In this blog, we have discussed clean room validation according to ISO 14644 guidelines.
What is a clean room?
The clean room is a specially designed sterile setting to minimize entry of aerosol particles and pollutants. It regulates pollutant level, humidity, and personnel access to prevent the entry of dust and germs. Medical device manufacturers need to have a clean room unit within their manufacturing facility. Notably, these rooms provide a controlled and sterile environment for manufacturing and packaging of medical devices. The rooms are specifically designed to maintain low environmental pollutant, such as dust, airborne microbe, aerosol particle, and chemical vapour, levels.
The major components required for constructing a clean room for medical device manufacturing factory are HVAC systems, cleanroom filtration unit, airflow pattern measurement system, and pressurization measurement system. These rooms have to effectively maintain a clean and sterile environment. Thus, they have to be regularly tested for their effectiveness to maintain the permitted particle count limit.
Furthermore, the clean room has to be properly validated for compliance with regulatory standards. The process of regularly assessing and monitoring the effectiveness of the clean room is vital. The cleanroom should be operating as required. Additionally, regular monitoring will help identify any potential contamination issues. Moreover, the cleanroom validation should be thorough and compliant with ISO 14644 guidelines.
The need for a clean room in a medical device manufacturing facility
The clean room provides a clean, regulated, and sterile environment. These environmental conditions are vital for assembling and manufacturing high quality medical devices. The clean room prevents the entry of both airborne particles and microbes into the regulated area. Airborne particles are harmful for hard drives and microchips used to manufacture medical devices. On the other hand, microorganisms will contaminate the medical devices, thereby making the devices a threat for patient safety. Thus, clean rooms are crucial for the medical device manufacturing facility.
Clean room validation
Validation of the clean room involves a series of mandatory tests conducted for assessing and monitoring the effectiveness of the clean room. The air quality, pressure, temperature, and other key parameters are evaluated during the clean room validation process. Moreover, medical device industry clean rooms are required to operate at the highest level of sterility and safety. The controlled and sterile environment is crucial for safely manufacturing and packaging medical devices. Contamination of medical devices while manufacturing them has to be avoided at all costs to ensure patient safety. Hence, clean room validation is a critical process for manufacturing sterile, safe, and effective medical devices. The clean room environment should meet stringent regulatory cleanliness standards.
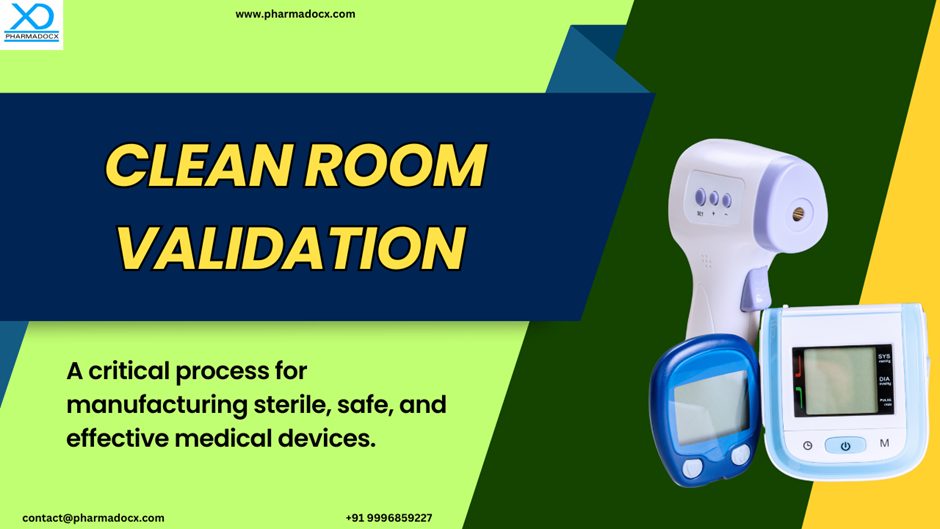
Essential tests for clean room validation
The ISO 14644 guidelines have laid down certain tests for the clean room validation process. These series of tests will effectively assess air quality, temperature, pressure, and other key parameters of the cleanroom. The guidelines mention the amount of particulate matter permissible in the clean room environment. For manufacturing sterile medical devices, compliance with clean room validation ISO 14644 guidelines is necessary. We have highlighted some of the tests that will help your medical device manufacturing facility clean room be ISO 14644 compliant.
- Airborne particle concentration level: The clean room airborne particle concentration has to be measured. A vital test in the clean room validation process is checking the concentration level of airborne particles and whether the particle size is within the limit. The purpose of this test is to evaluate the air cleanliness classification with respect to airborne particles in the cleanroom. The airborne particle size should be within the range of 0.5 μm and 5 μm. Moreover, the tests should be performed according to ISO 14644-1 guidelines. Furthermore, the at-rest state tests should be based on the limits specified in Table 1 of ISO 14644-1. On the other hand, the operational state tests, should be based on the WHO guidelines.
- HEPA filter leakage evaluation test: Cleanroom filtration units commonly have high-efficiency particulate air (HEPA) filters. The HEPA filters can effectively remove 99.97% of the airborne particles up to a size of 0.3 microns. The proper installation and integrity of the air filter system has to be evaluated. The HEPA filter leakage evaluation test checks for any defects and bypass leakage in the filter. The leak detected should not be exceeding 0.01%. The HEPA filter leakage evaluation test protocol should follow the ISO 14644-3 guidelines. An aerosol challenge should be introduced upstream of the filter, followed by a downstream scan.
- Temperature and humidity level test: The regulatory guidelines require the clean room temperature be maintained between 18 °C to 22 °C and relative humidity should not exceed 65%. This test focuses on ensuring the clean room’s temperature and humidity level are within the stipulated limits. The test protocol should follow ISO 14644-3 guidelines.
- Air change rate test: This test aims to assess the volume of air supplied to the cleanroom per unit of time. The air change rate should be 15 to 20 times per hour or as stated in the regulatory guidelines. The supply air volume flow rate in non-unidirectional cleanrooms is measured. The test protocol should follow ISO 14644-3 guidelines.
- Recovery test: This test aims to assess the time required for the cleanroom to return to its target cleanliness levels after a disturbance. The test protocol should follow ISO 14644-3 guidelines.
- Air pressure difference maintenance test: The cleanroom air movement system’s capability is verified in this test. The test aims to evaluate the clean room’s ability to maintain the specified air pressure differential. According to the ISO 14644-4 guidelines, the air pressure differentials should typically range between 7.5 Pa and 15 Pa. The air pressure difference maintenance test should be performed during validation and daily routine monitoring.
Points to keep in mind while designing a medical device clean room
We have to keep in mind the following points while planning the clean room design.
- Determine the level of cleanliness required for your factory.The medical device clean room cleanliness level will depend on the products being manufactured or assembled in your factory.
- An air filtration system appropriate for the cleanliness level will be required.
- In-depthprotocols for maintaining the sterility and cleanliness of the clean room have to be formulated.
- A control area outside of the clean room where personnel can prepare for entry into the room is required.
- It is important to wisely select the location of the clean room for medical device. It should be located away from sources of contamination, such as windows and external doors.
Pharmadocx Consultants: Your trusted clean room validation partner
We provide comprehensive support for clean room validation according to ISO 14644 guidelines. Our team has extensive knowledge of the regulatory guidelines. We will leverage our expertise to help you navigate through the complexities of the validation process. Additionally, we design clean room for medical device manufacturing facilities as per international standards and norms. To avail our clean room design and validation service, drop an email at [email protected] or call/Whatsapp on 9996859227.